The face of welding
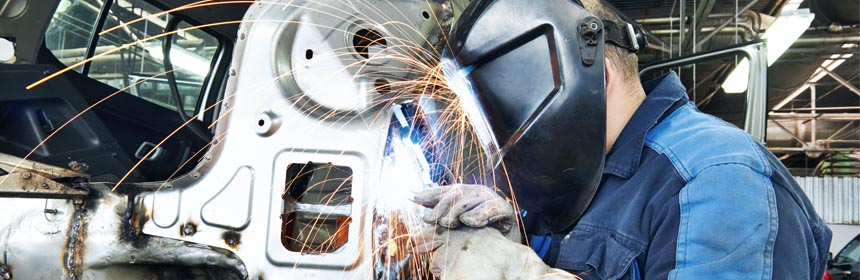
- 29/10/2015
- Posted by: Simon Wait
- Category: Magazine
With a variety of different joining methods included on modern vehicles we take the time to talk to various industry experts to understand a little more about each, along with the benefits and challenges they offer.
Over the past 10 years the car industry has seen a shift in focus, with manufacturers becoming more environmentally aware. Government legislation and pressure from the European Union (EU) has forced car manufacturers to make vehicles more efficient to reduce the carbon footprint. In response, car makers are designing car bodies that are lighter in weight. In order to do this, a combination of materials such as steel, high strength steel, ultra-high strength steel, aluminium, plastics and composites are all a part of their designs now.
As these different materials can’t be welded together, bodyshops are now seeing more and more panels being glued and riveted together. This in turn has led to several new riveting tools and riveting methods being introduced.
With the repair market accepting that bonding and riveting will be a major repair method, Bodyshop Solutions Ltd has launched the XPress800 Modular repair system. This modular approach allows for a versatile riveting system, that gives every repairer one tool that is capable of fitting all types of rivets, rather than the repairer having to buy a separate tool for each new rivet type.
Riveting
Most premium car manufacturers are now using rivet and bond to attach dissimilar metals such as aluminium to steel managing contamination/corrosion. And there is also a necessity to provide equipment to carry out the reverse to remove panels joined with this process. Rivet removal and heat induction equipment is therefore ideal.
Tony Young, operations director, ITAS said, ‘There is no longer such a thing as a generic repair and this has brought challenges, with bodyshops needing to invest in continual training which keeps technicians up-to-date with the latest methodologies and to provide the correct tools to guarantee a safe and compliant repair.’
ITAS instructs using the methodologies specified by its manufacturer partners. ‘Our welding and joining courses take place at our new 33,000sqft Training Academy in Milton Keynes which contains cutting-edge equipment and technology, hand-picked to give technicians the right tools to follow the right standards to make the right repair. We have isolated welding facilities including a high-specification area for completing panel training in an ideal environment, free from distraction,’ said Tony.
Technicians practice on sill sections which are designed using the same materials and construction as the road-going vehicle and make their repairs using the approved rivets and bonding materials. Repaired sections are kept on file and tested on an ongoing basis to verify quality and durability.
Training
Tony continued, ‘This attention to detail is critical, manufacturers spend millions of pounds investigating and compiling methods to ensure a safe repair and ITAS plays its part by delivering training which upholds the duty of care on behalf of the manufacturer, the bodyshop and the insurance company.’
The rapid pace of development within vehicle manufacturing is here to stay. We are already seeing increasingly lightweight materials which increase fuel efficiency – a trend which will continue as the electric vehicle market grows – and this means new standards, new methods and a continued emphasis upon training. As vehicle construction changes, the needs of the market must adapt to meet the same level of technology.
‘Looking ahead, I see more specialisation within bodyshops, a greater need for manufacturer-specific training and an increasing focus on professional apprenticeship schemes which create the highly-skilled technicians of the future,’ added Tony.
Welding
According to Mark Swaby, chairman of Bodyshop Solutions, ‘Bonding and riveting are becoming more and more relevant in the repair industry, this is leading to a reduction in the amount of welding being undertaken by repairers, which in-turn has a knock-on effect on the welder manufacturers, who in the future are probably unlikely to make any more advances in specifications for the spot welders or MIG/MAG welders. It is likely therefore that 14,000amps will be the maximum required for spot welding. Inevitably, bonding and riveting will be the favoured repair method in the future, as we see more rivets and less welding in the workshop.’
Bodyshop Solutions Ltd. is an industry supplier that currently offers products and training for the welding and joining sector, Mark Swaby added, ‘We offer a comprehensive all-in one service to the bodyshop industry. Our products include spot welding equipment, MIG/MAG welding machines for both steel and aluminium, welding consumables, a comprehensive range of bonding and riveting tools, British Standard weld testing and high strength steel awareness courses, as well as on-site servicing and calibration for all the equipment sold.’
Mark commented that Bodyshop Solutions provides full product training and certification on every piece of equipment and once customers have invested money in its products ‘it is up to us to show them how to get the best results and value from their investment.’
According to Neil Pulsford, UK commercial director at GYS, the industry is still many years away from discarding traditional welding methods, so the pace of change seen in the bodyshop is gradual. Financially bodyshops are challenged to balance their equipment investments carefully, as it will be necessary to follow manufacturer methods carefully with the use of correct welding/riveting equipment for many years to come.
Mixture
Neil said, ‘Over time repair equipment specification increases to handle new steels. Identification of these steels can be an issue for the repairer. From an equipment perspective, GYS now produce spot welders with fully automatic modes removing the need for steel identification and capable of delivering 14,500amps though this exceeds current repair requirements.’
Neil continued, ‘Some manufacturers (eg GM) use a mixture of spot welding and weld through panel bond, this requires a glue setting (pre-burn) from the spot welder. Panel joining by brazing requires specialised equipment capable of operating smoothly at low amperage sometimes as low as (15amps). Welding aluminium requires good temperature and the expanded use of aluminium in vehicles is now driving a requirement for pulse MIG welders in bodyshops.’
It’s clear to see that a lot of pressure has been put on the bodyshop industry in terms of keeping up with the latest repair methods and the equipment needed to carry out repairs, thanks to innovation and the new materials being introduced to the automotive sector. After speaking to industry insiders though it’s obvious that the two most important things to consider in regards to welding and joining for the future, is investing in proper training and the right equipment. Bodyshops that wish to keep up with the fast pace of auto industry must ensure staff are trained in the correct/recommended repair methods and that they have the correct tools in order to complete an effective and safe repair.